Overhead crane accidents can result in catastrophic loss of life or property. They are also costly to businesses in terms of lost time, repairs, and other expenses.
According to ASME standard B30.2, a company’s management team trains crane and hoist operators. This could include equipment manuals, government training materials, courses, seminars, and literature. Click OSHA Overhead Crane Training Requirements to learn more.
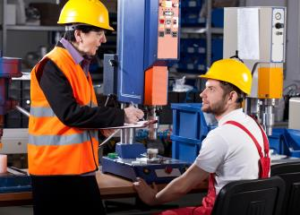
Crane accidents can cause significant human and financial losses. In a recent 10-year study, OSHA reported that the average cost for an accident that involved cranes was two million dollars. This reflects not only the costs associated with injuries or fatalities but also lost productivity. Many of these incidents could have been avoided if more training had been conducted for the operators who operated the equipment.
To mitigate risks, cranes should be thoroughly inspected before each use. This includes checking for signs of wear and damage, as well as making sure all safety features are functioning properly. The inspection should be done by qualified personnel who are familiar with the manufacturer’s specifications and load charts. It is important to make note of any recurring problems and take steps to correct them.
One of the most common causes of accidents is overloading. This can happen when a load is dropped, swings or drags, or when the hoist exceeds its capacity. While the risk of this can be reduced with proper planning, inspections and proper rigging techniques, it is still possible that an operator will accidentally overload the crane, which can have devastating consequences.
For this reason, the Occupational Safety and Health Administration (OSHA) requires crane operators to receive specific training before operating the equipment. This training can be provided by a variety of sources, but it should always meet OSHA and ASME (American Society of Mechanical Engineers) guidelines.
In addition to providing training, a qualified crane training company should also conduct regular inspections of the equipment and provide detailed reports. These reports should include both the results of the inspection and a list of any recommendations for corrective action. A third-party inspection company is a great option for this purpose because it can offer several benefits, including impartial reporting, specialized expertise, cost-saving recommendations and adherence to state regulations.
Another benefit of working with a third-party inspection service is that they can help you establish the qualifications of your employees as competent persons to perform annual crane inspections. As explained in the ASME B30 standards, this means that the individual must have knowledge of the crane’s operation and its capacities. The individual can be an employee of the employer or the operator-in-training, but he or she must have direct line of sight and communication with the person operating the crane.
Load Block and Safety Latch Inspections
When it comes to working with hoists and cranes, safety and training are key. Untrained or inexperienced operators are a danger to themselves, their coworkers and the products they lift. Many facilities and employers will ignore the need for proper training altogether or rely on on-the-job experience to qualify their workers. This may work if no accidents occur, but it’s not a long-term solution for any operation that relies on cranes or hoists.
According to ASME B30.2 Section 2-3, a person who operates a crane “SHALL be trained.” This means that even maintenance employees or people in supervisory roles will need to attend training. A crane is a dangerous piece of machinery, and training should be provided to anyone who will be operating it, even those who have already received on-the-job training.
Crane operator training includes learning about pre-operation inspections and signaling. During these inspections, the equipment must be checked for any signs of excessive wear or damage. The equipment must also be tested to see if it’s functioning properly. This means that the wire rope is not frayed or twisted and that the travel limits and hoist limit switches are operating as they should.
The inspections also include examining the hook latches. These latches ensure that loads are secure when being maneuvered. If any of the latches are faulty, they must be repaired or removed from service. The safety latches must be able to bridge the throat opening of the hook in a closed position and lock loads in place. The load hook should have a latch marking that is visible and the pin must be in good condition.
A faulty or damaged hook can cause an accident, especially if it’s not secured. This is why it’s important to inspect the hook before each use. Look for any nicks that you can fit your fingernail into and any rust or corrosion. Any nicks that are too large can create a hazardous condition.
Another aspect of the inspection is looking at the size of the load. The load should never be larger than the crane’s structural capacity. This could cause an overloading event which is a common cause of crane accidents. One of the best ways to prevent this is with a proper load sizing system.
Control Pendant Inspections
While radio control systems have become more popular with overhead cranes as their prices have dropped, wired pendant controls are still used in many applications. These systems allow the operator to stay near the load and can work well for straightforward operations that don’t require complex movements of the load. Wired pendant systems should be inspected for proper operation and safety.
This includes checking push button labels and motion direction, ensuring that the upper limit switch is properly wired for hoisting, and that the pendant is in working order. It’s important that the pendant is free of zip ties and other potential hazards that can cause electrical shock. In addition, it’s important to perform a functional test of the pendant prior to starting each shift. A simple inspection checklist can be laminated and zip tied to the pendant to remind the operators to perform these important checks on a daily basis.
If you’re using a wired pendant, you should also regularly inspect the pendant cable for any damage or signs of wear and tear. In particular, check the pendant cable length to ensure that operators are able to maneuver in their workspace without creating trip hazards or being blocked by the cable. If you find that the pendant cable is too long, it’s important to consider alternatives, such as a remote control unit or a different wireless system.
The ASME B30.2 safety standard specifies that crane owners and managers must not hire anyone to operate a crane until they have passed both a written and practical examination, as well as received training and demonstration of their knowledge and ability. This training is specific to the equipment and application in question, so that a person has the skills needed to operate that particular type of crane.
Even with formal training, it is important to remember that receiving a certification does not automatically qualify someone as a qualified or competent crane operator. That responsibility still falls on the employer to determine if an employee has the experience and skills necessary to operate a particular piece of equipment.
Walkway and Site Inspections
Overhead cranes are essential in the construction and manufacturing industries, but they can also be dangerous. That’s why it’s important to have proper training, follow safety regulations and standards, conduct regular inspections and maintenance, and use personal protective equipment (PPE) when operating these powerful machines. If you’re looking to complete overhead crane safety training, there are numerous courses available. However, it’s important to find a course that meets OSHA and ASME requirements. This way, you can be confident your training will be complete and compliant.
An overhead crane safety training program should include an overview of OSHA’s rules and regulations regarding these machines, the types of inspections required, and best practices for preventative maintenance and safe operation. Following these guidelines will help you keep your employees safe and your equipment running smoothly, avoid costly repairs, and save money on energy costs and downtime.
Cranes require frequent inspections to detect any malfunctioning, deteriorated, or worn components. Some of these inspections are conducted daily or monthly, while others are more comprehensive and take place at least once per year. The type of inspection you need to perform will depend on how frequently you use your crane system and how often it is exposed to weather or wear and tear.
When a crane or hoist system is not properly maintained, it can lead to a variety of issues, including equipment failures, injuries, and even fatalities. If you’re not following proper maintenance and inspection procedures, your company could face citations from OSHA and other governmental agencies. In addition, injured workers will incur medical expenses, lost productivity, and increased worker’s compensation insurance rates.
When you invest in proper overhead crane maintenance and training, your company will reap the rewards. In addition to reducing the risk of injury, you’ll also reduce your worker’s compensation claims and legal expenses. And, since a majority of crane accidents are caused by operator error, investing in specialized training is a good business decision for any facility.